
Baltic Robotic Operation Systems
Meet M1N3R
Our robot for the 2015 BEST Robotics Compeition is complete! BROS is proud to present: M1N3R!
After a few names were tossed around we chose a name. We wanted to relate our robots name to the game theme of Pay Dirt. The “1” and “3” replace the letters “I” and “E”. We have robot that is capable of performing tasks: repair the damaged mine components, collect core samples, and collect various minerals.

Final Robot Design
Our robot design begins with the base—a plywood box with a hollow interior that holds no purpose other than to hold the components of the robot together. Inside the box is the drive system of our robot (two fully contained motors and four wheels extruding from the top and bottom of the box via small slits). The rear wheels are simple wooden circles wrapped in a rubber-based foam to provide extra traction. These wheels are mounted to motors using metal motor mounts. The front two wheels are wooden octagons with inset strips of PVC pipe along the edge. The PVC pipes act as small wheels along the larger wheel. This allows for our robot to slide side to side when turning but still giving us the needed traction while driving forward. The front wheels are mounted onto fixed metal rods.
On top of our base lies the Vex Cortex and the arm of our robot. The cortex is centered in the middle of the base and all the wires are connected to control the functions of our robot. Most of the wires are rerouted inside of our plywood box. This was used as an attempt to eliminate wires cluttering. M1N3R’s arm is positioned at the very front of our robot and is quite complex. The base of the arm is a large PVC “H”, allowing the arm to pivot along the crossbeam and freely rotate. Attached to the arm is a large plastic gear, nearly six inches in diameter. Connected to the large gear by a pulley—mounted a few inches back on the base—is a motor with a much smaller gear. This motor functions to rotate the arm. The pulley system gives our arm a huge mechanical advantage and gives it the strength and precision required to perform well. The beginning of the arm is attached to the front of the pivot block.
A small motor is connected to the front of the pivot with a homemade aluminum bracket that extends away from the robot. Using this small, homemade motor mount, we can interchange different lengths of PVC pipe—changing the length of the arm. Our claw is basically a small box shaped collection of aluminum with a servo in the middle of it. This servo allows for the claw to open and close while taking up virtually no space and also adds support to the structure of our claw. The claw is lightweight and can be mounted to the small piece of PVC pipe that juts out from our motor. Because the claw contains only a single servo and minimal aluminum, it reduces the stress on the rest of the arm.
Above the base and arm is a large polycarbonate chute. The chute is essentially a single piece of translucent plastic that raises from the edge of our base to the front of our robot at a 40 degree angle. The front of the chute is approximately 10 inches high. This is the perfect height to allow our arm to drop things into it. The sides of the chute are attached using small aluminum brackets and are placed at a 45 degree angle. The angled sides were used to avoid commodities falling off the side. The falling pieces will inside slide into the trailer. Below our chute is a single servo attached to an aluminum hook that connects our trailer to the rear of our robot.
The trailer is a completely detached subunit of our robot and can be separated from the rest of the robot using a small servo. The base of our trailer is an eight inch square of plywood. Aluminum tracts are attached to the bottom similar to a bobsled. On the back of the trailer is a sheet of polycarbonate. This allows our driver and spotter to see into the trailer. The sides of the trailer are made of aluminum brackets that extend outwards at a 45 degree angle. Electrical tape is strung across these brackets, creating a flexible, lightweight barrier to hold materials. Because the sides extend outwards, our robot is able to catch more falling materials. The front of the trailer is made up of a single sheet of aluminum and is bent towards the robot, allowing materials from the chute to tumble directly into the trailer. A small square is cut out of the front of the trailer to allow a servo powered hook to slide into, thus connecting the trailer and the robot. This allows the robot to migrate about the field while pulling the trailer.
Strategy
Our robot design team met early to decide which methods of point collection we found the most worthwhile and then decided which elements we wanted our robot to focus on. Our strategy relies heavily on the fluctuation of the market shift throughout the competition, the abilities of our drivers, and the amount of risks we are willing to take each round in order to score maximum points. We designed M1N3R to perform a specific route that our team agreed was the best way to score points.
Starting the round, M1N3R will be attached to our trailer and we will immediately drive to the replacement air filter. Our robot will grab the filter using the claw—this may require temporary detachment from the trailer. With the both the trailer and the air filer, our robot will proceed to score the filter in its box within 45 seconds. Our robot will then rotate, so the trailer is released directly below the magnetite chute. Using the back of our robot, we can wedge under the pipe holding the magnetite. By driving forward the pipe will raise and spill its contents into our trailer. Our robot will then quickly reconnect with the trailer and continue on. The robot will drive to the coal chute next, activate the lever that drops the coal, and collect the falling coal in our trailer. Any remaining pieces of coal can be picked up off of the floor by our claw. M1N3R will then begin its journey back to the starting zone. Our trailer can be easily detached in the starting zone, where our spotter will take control by sorting the components into their respective bins. Any leftover time will be used to collect any miscellaneous commodities, such as aggregate or more coal.
Depending on the market shift, there is a possibility that our strategy could completely change. Our robot is able to obtain chalcopyrite samples as well as core samples from the third sublevel if deemed necessary, but we do not want to risk going that far into the mine during every round.
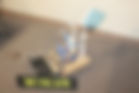
Click to enlarge!